こんにちは!武庫川女子大学多田ゼミの高見と田所です!
前回の記事では、製材所での見学の様子から、1つ目の施策を作るところまでをご紹介しました。今回は、その施策をベースに改良したコンテナの試作品を自分たちの手で作成する工程に入りました!
1. 図面から木材へ
設計した図面をもとに、側面を家バージョン、雲バージョン、街並みバージョンなどといろいろな形を設計し、それをショップボットを使って木材を切り出しました。
2. 端材をカット
パーツや端材を取り外すために、トリマーを使ってカット作業を行いました。加工場では、自作の加工台にトリマーをセットして使っていて、その知恵になるほど!と驚きました。トリマーを使うのは初めてだったので、最初はとても緊張しましたが、作業を進めるうちに徐々に慣れていきました。
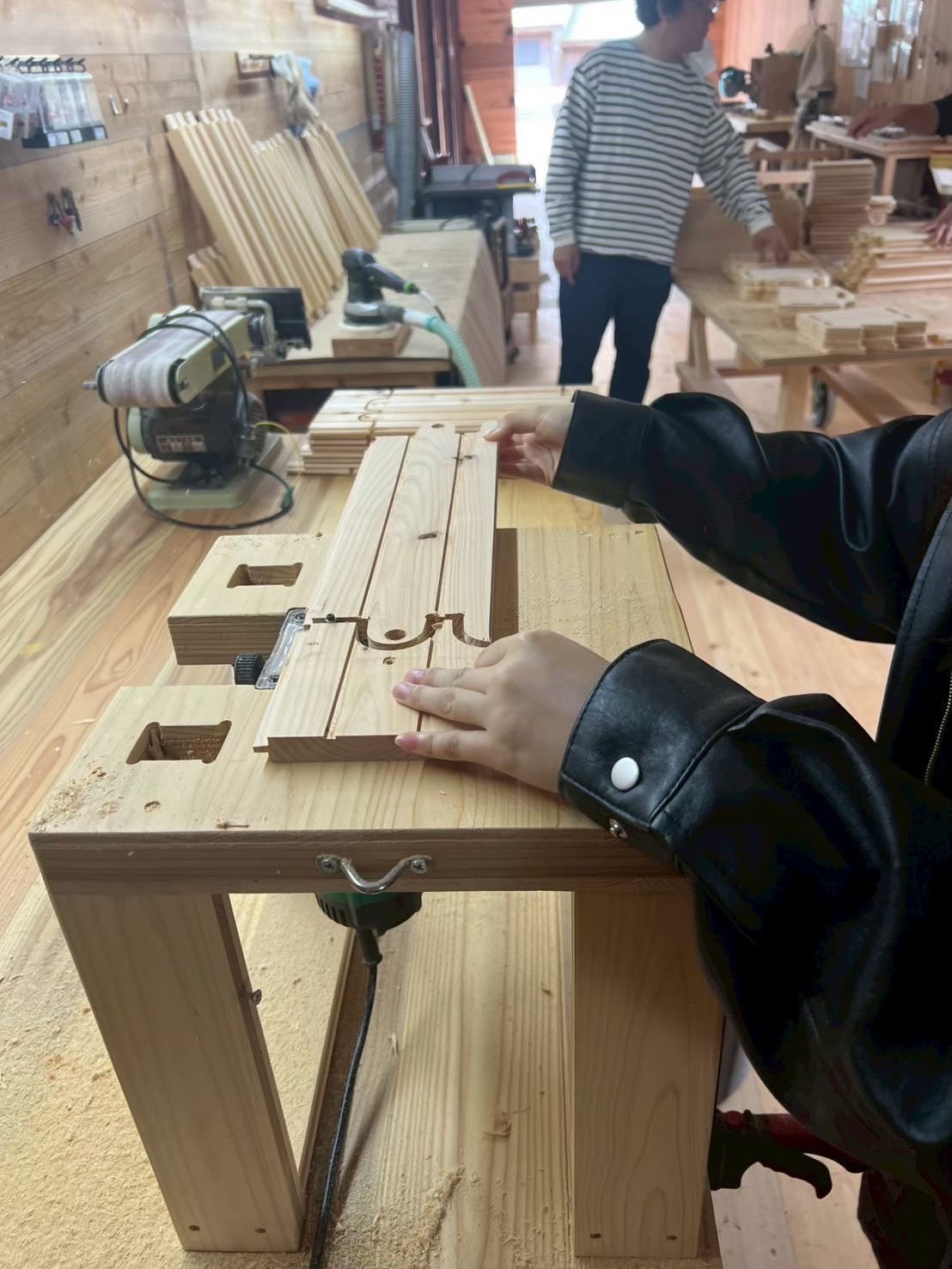
3. 面取りをする
ショップボットで加工した際、穴の部分や外側の輪郭がやや粗かったので、先ほど使用していた電動ノコギリの刃を交換し、面取りをしました。面取りとは、木材などの角を丸くすることです。面取りをすると角が立っていたときよりも全体の印象が柔らかくなり、子どもが使っているのを想像させる可愛らしさが感じられる仕上がりになりました。
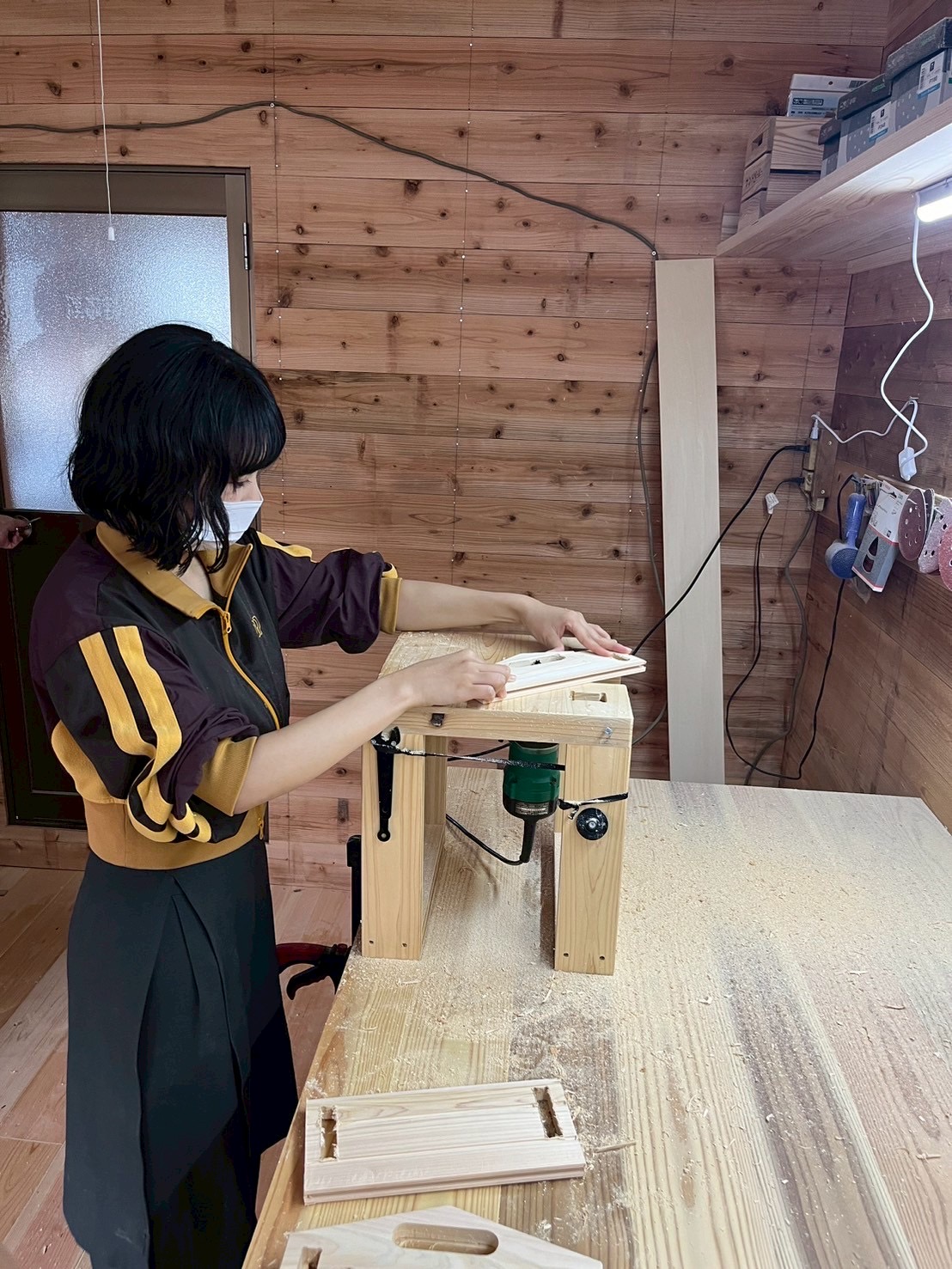
紙やすりでバリをとる
トリマーでは削りきれなかった細かなバリを、紙やすりで丁寧に磨いていきました。角を丸く整えていく作業は地道で、長時間続けていると腕がぱんぱんになりました。でも、表面がさらにつるつるになっていくのが嬉しくて、つい夢中になっていました。特に持ち手の部分は、紙やすりだけでは難しかったので、ベルトサンダーも使いながら仕上げました。
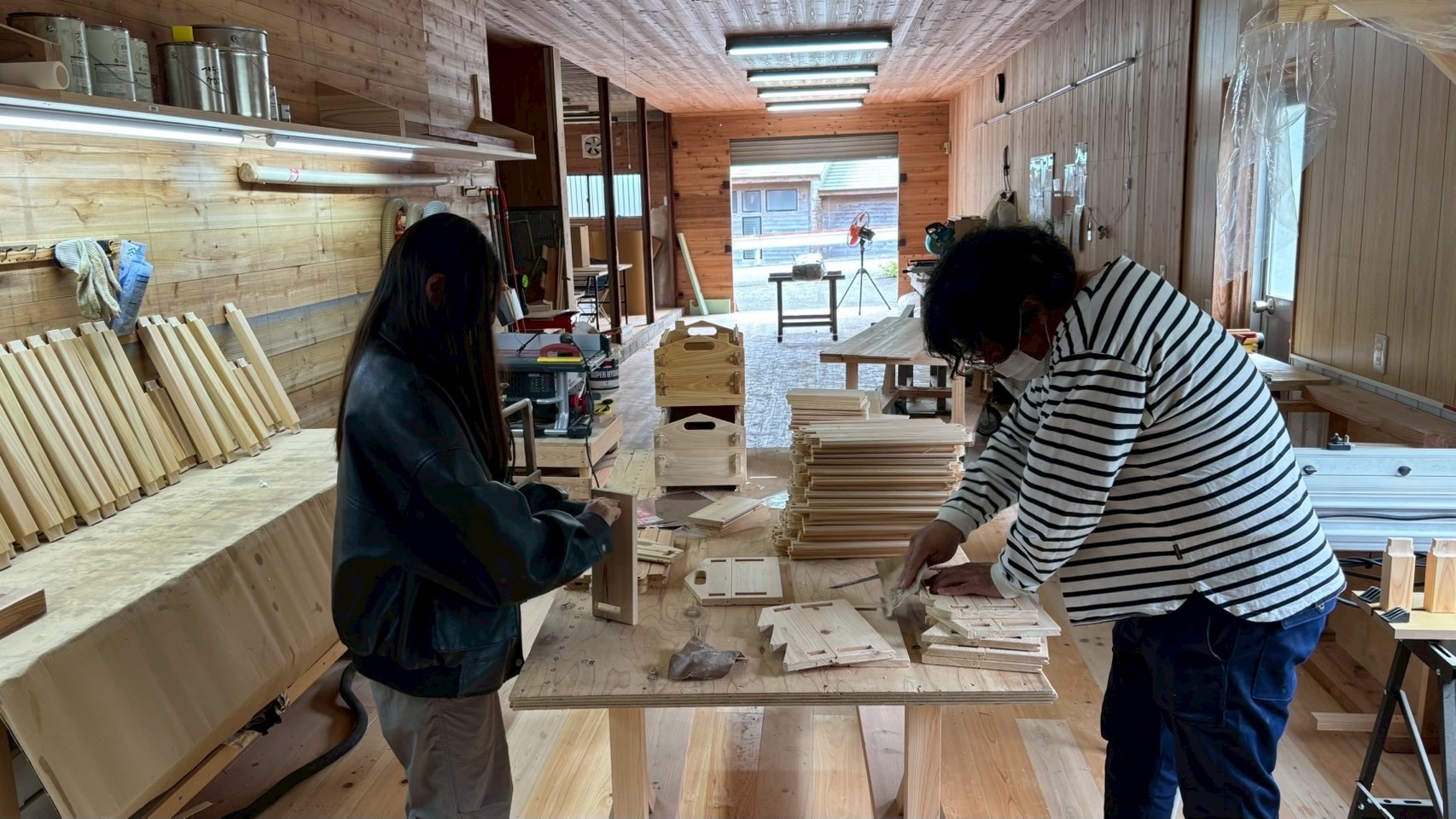
組み立て
最後は、すべての部材を組み立てる工程です。
しかしここで、設計段階ではぴったりはまっていたはずの部品が、木の個体差や癖の影響でうまくはまらないというハプニングが発生しました。
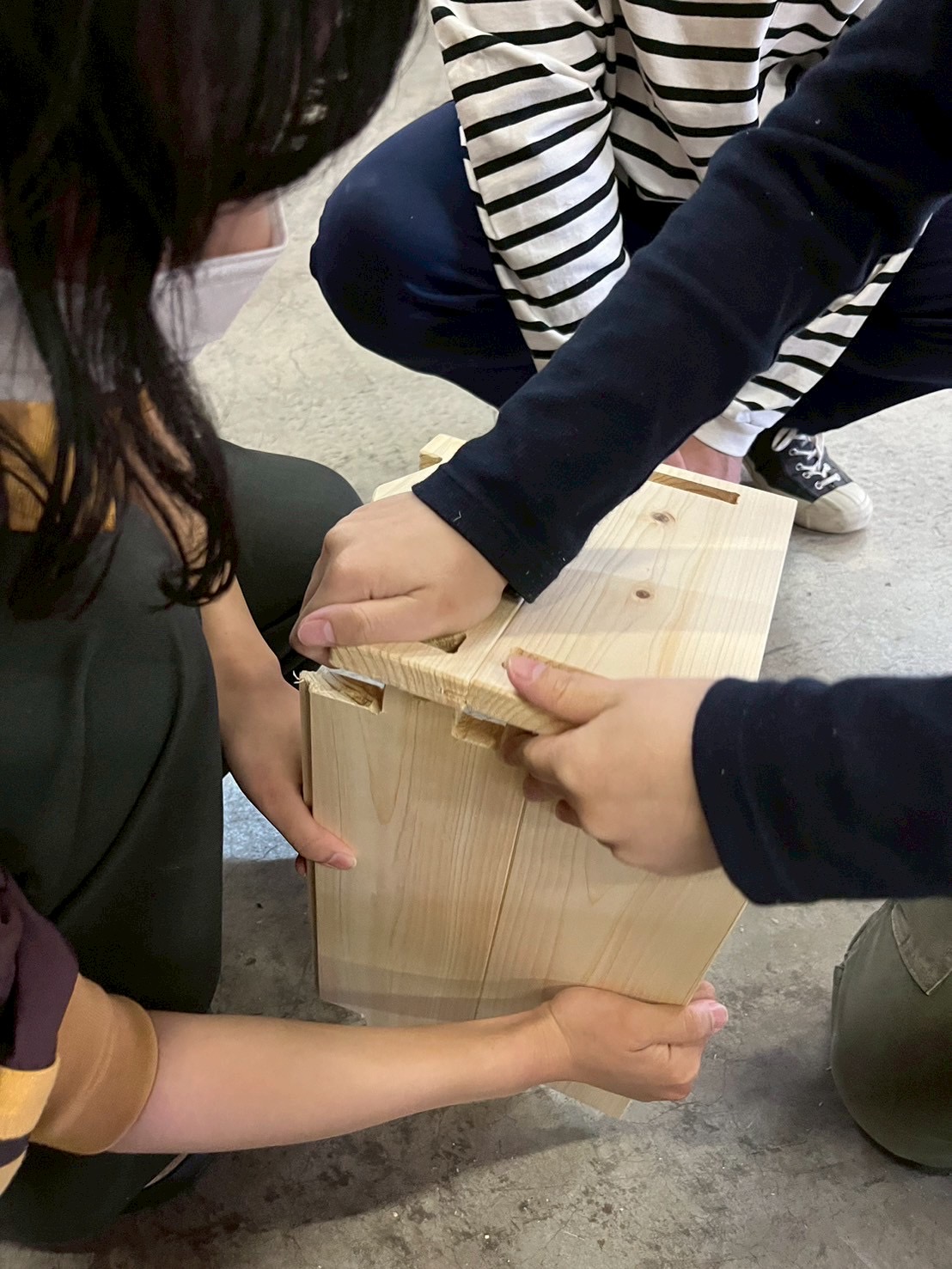
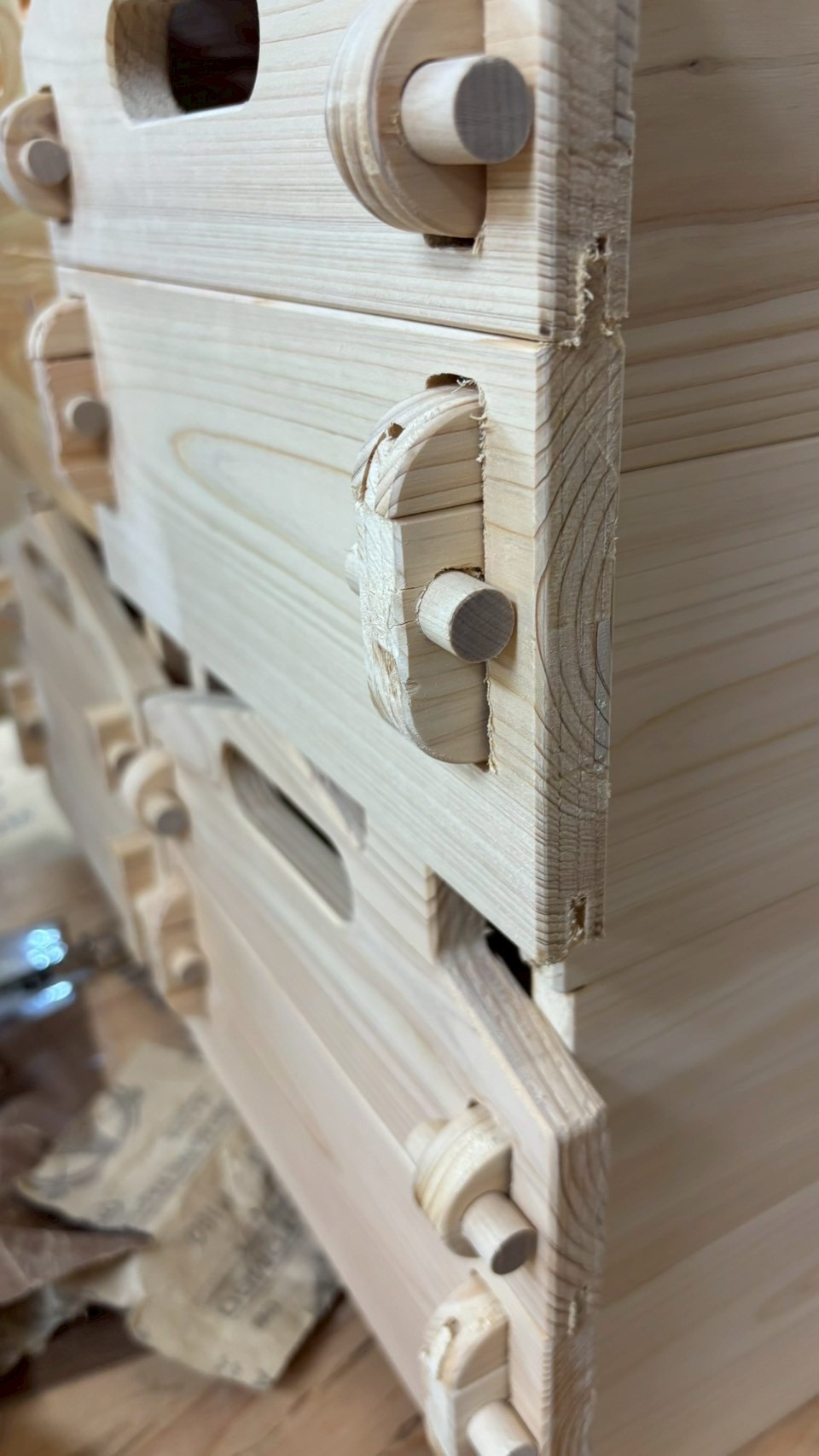
そこで、穴をトリマーで少し削って拡げたり、ワイドベルトサンダーで側板を薄くするなど、現場で工夫しながら調整を行いました。
また、ダボも金槌を使わないと入らないほどきつく、無理に叩き込むと繊維方向に木が割れてしまう場面もありました。こうしたトラブルを経験する中で、改良のヒントも見えてきました。
例えば:
- ダボの穴を楕円形にして、繊維方向への負担を軽減する
- 穴をやや緩めに設計し、金槌ではなくボンドで固定する
6. 梱包
最後に、実際に商品化する際の梱包方法を試してみました。セット販売の梱包方法として、部品がバラバラにならないよう、ラップで巻いてみました。梱包したものを並べてみると様になっているような気がします!
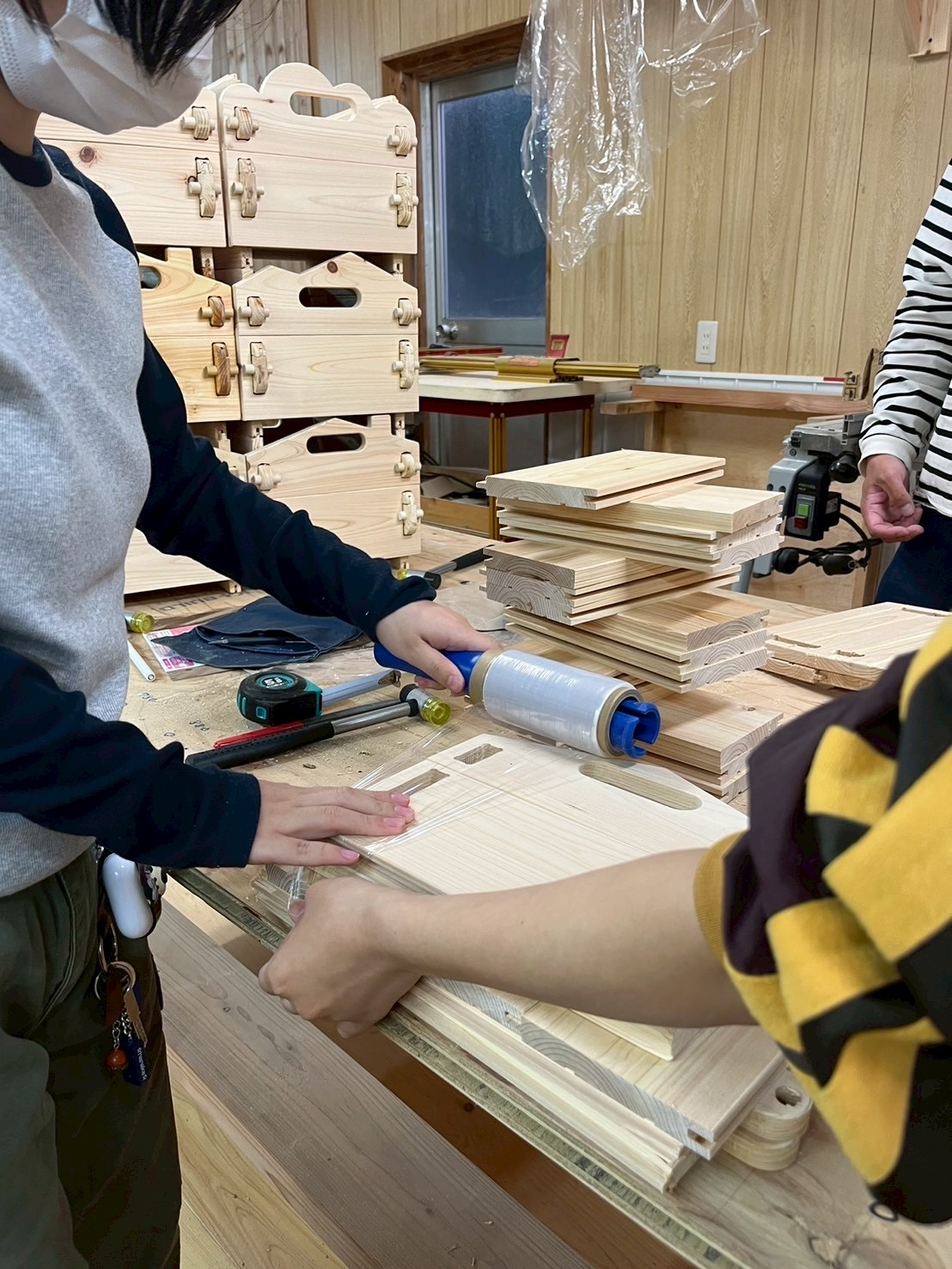

このような細かな工夫の積み重ねが、製品の完成度や使いやすさに大きく関わってくることを、実際に手を動かすことで実感しました。